Centrifugal Pumps
Introduction centrifugal pumps:
Centrifugal pumps are indispensable in numerous applications, particularly in water supply systems, where they function as the heart pumping blood through veins.
Today, let’s delve deep into understanding centrifugal pumps inside out.
1.Essential Equipment in Chemical Production
Centrifugal pumps are integral to chemical production due to their versatility in handling various performance parameters such as flow rate, head pressure, and compatibility with different media. They boast compact size, simple structure, ease of operation, uniform flow, long lifespan, and cost-effectiveness, making them a staple in the industry.
2.Basic Structure and Working Principle
2.1 , Impeller Working Principle
To understand the fundamental structure and working principle of centrifugal pumps, we focus on the theme of converting kinetic energy into static pressure energy.
Centrifugal pumps utilize the centrifugal force generated by the high-speed rotation of the impeller to extract liquids or other materials. They find extensive applications not only in industrial settings but also in agricultural irrigation, municipal water supply, power plant circulation systems, urban pollution treatment, and more.
2.2, Basic Structure of Centrifugal Pumps
The primary components of centrifugal pumps include the high-speed rotating impeller and the fixed volute-shaped pump casing. The impeller, usually equipped with several backward-curved blades (typically 4-12 blades), is securely mounted on the pump shaft and driven by a motor to rotate at high speed.
- The impeller performs work on the liquid inside the pump.
- It serves as the energy supply device for centrifugal pumps.
- The central suction inlet of the pump casing is connected to the suction pipeline.
- A non-return foot valve is installed at the bottom of the suction pipeline.
- The discharge outlet on the side of the pump casing is connected to the discharge pipeline.
- The discharge pipeline is equipped with a regulating valve.
2.3,Working Principle of Centrifugal Pumps
When the centrifugal pump is started, the pump shaft drives the impeller to rotate at high speed, forcing the liquid pre-filled between the impeller blades to rotate. Under the action of inertial centrifugal force, the liquid moves radially from the center of the impeller to the outer periphery.
As the liquid passes through the impeller, it gains energy, increasing static pressure and flow velocity. When the liquid exits the impeller and enters the pump casing, it gradually decelerates due to the widening flow passage inside the casing, with some kinetic energy being converted into static pressure energy before entering the discharge pipeline tangentially.
- The volute casing collects the liquid discharged from the impeller.
- It acts as an energy conversion device.
- When the liquid is thrown from the center of the impeller towards the periphery, a low-pressure zone forms at the center of the impeller.
- Due to the potential energy difference between the liquid level in the reservoir and the impeller center, the liquid is drawn into the impeller center.
- With the continuous rotation of the impeller, the liquid is continuously drawn in and discharged.
- The mechanical energy gained by the liquid in the centrifugal pump ultimately increases static pressure energy.
It’s important to note that if the centrifugal pump is not filled with the liquid to be transported before starting, low air density results in insufficient centrifugal force generated after the impeller rotates. The low-pressure zone at the impeller center is unable to draw in the liquid from the reservoir. Therefore, even if the centrifugal pump is started, it cannot transport the liquid. This phenomenon is known as air binding.
Installing a non-return foot valve in the suction pipeline prevents the liquid filled into the pump casing before starting from flowing out of the casing. The presence of air in the suction pipeline into the pump casing can cause air binding.
3. Principle of Centrifugal Pumps
This section will cover the definition of centrifugal pumps, their construction, and their operational principles.
- A centrifugal pump is a type of hydraulic machine.
- It converts mechanical energy into hydraulic energy using centrifugal force.
- The pump employs rotation to impart velocity to a liquid, transforming it into a flow.
- Every centrifugal pump consists of mechanical components essential for its operation.
- These components include the pump shaft mounted on bearings.
- There’s also a sealing mechanism to prevent uncontrollable leakage.
- Structural components are designed to withstand the loads and stresses encountered during pump operation.
- Wear surfaces allow the pump to maintain and return to its original specifications.
Components of Centrifugal Pumps
Every centrifugal pump should include the following components:
- Shaft
- Impeller
- Casing
- Suction Pipe
- Delivery Pipe
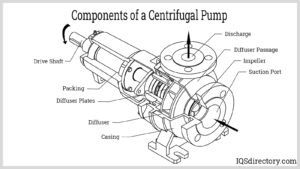
4.Manufacture of Centrifugal Pumps
When choosing materials for centrifugal pumps, several factors must be taken into account. These include strength, resistance to abrasive wear, corrosion resistance, casting and machining properties, repair and welding capabilities, and cost considerations.
Materials Used in Centrifugal Pumps
Various materials are used in the construction of centrifugal pumps, including:
- Cast iron – Most commonly used due to its high tensile strength and abrasion resistance, suitable for high-pressure applications, and durable.
- Stainless steel – Particularly austenitic stainless steel, favored for its corrosion resistance, high tensile strength, and suitability for chemical pumps.
- Cast steel – Suitable for high-pressure conditions, offering good mechanical properties, though not as corrosion resistant as certain stainless steel grades.
- Carbon structural steel – Widely used for pump shafts where corrosion resistance is not required.
- Alloy steel – Utilized for high-strength pump shafts.
- Non-metallic materials – Primarily used for sealing purposes, including polytetrafluoroethylene, rubber, nitrile rubber, and fluorine, offering high temperature resistance and corrosion resistance.
- Bronze – Used for pump bodies, aiding in sealing. Tin bronze is common for larger pumps, while nickel aluminum bronze offers superior corrosion resistance and mechanical properties but is costlier.
- Composite materials – Employed to enhance chemical resistance, such as rubber linings in the volute, graphite monolithic ceramics, and pumps for corrosive liquids like hydrofluoric acid.
These materials are also used in the manufacture of pump bodies.
Any more details, kindly contact us thanks.